
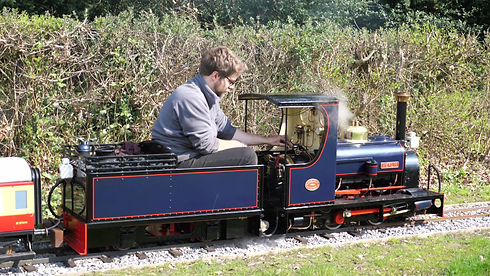
How to Stop a Train with PNP Railways Vacuum Brakes:
A Step-by-Step Guide
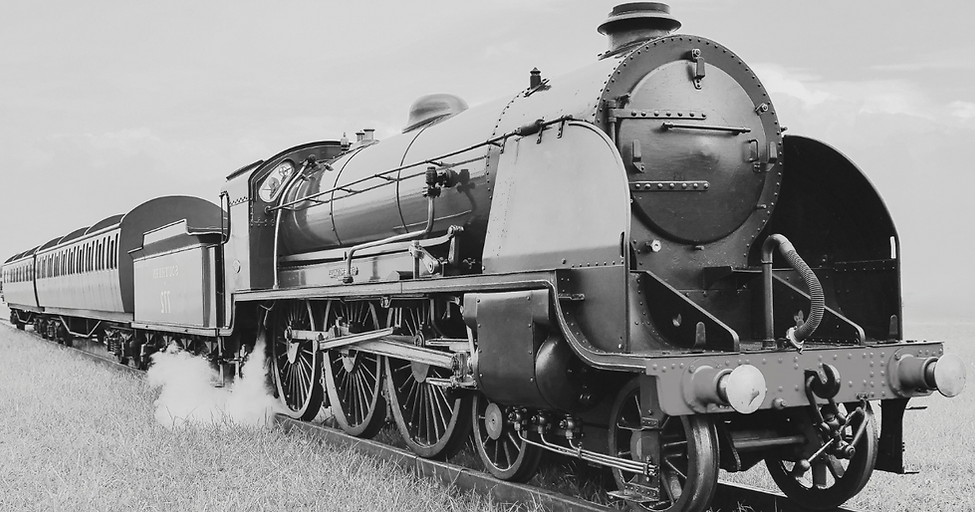
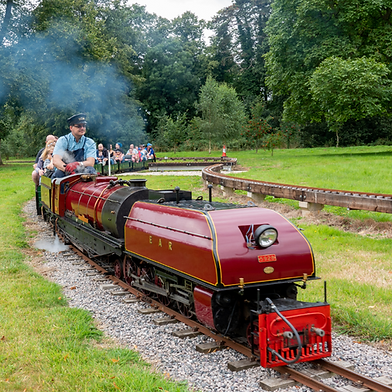
"Vacuum brakes were once a common type of braking system used on trains, particularly steam locomotives"
While vacuum brakes are not as commonly used today in full-size, they remain an important part of rail history and are still used. especially for stopping a model train.
If you're interested in learning more about vacuum brakes and the PNP Railways vacuum brake system, this step-by-step guide will provide you with all the information you need.

"From Handbrakes to Vacuum Brakes: A Brief History of Revolutionizing Train Braking Systems"
In the realm of railway safety, the development of braking systems has played a pivotal role in preventing catastrophic accidents. Vacuum brakes, a significant innovation in the 19th century, revolutionized the way trains came to a halt. Vacuum brakes made their debut with the granting of patents in Britain in 1844 and America in 1872. However, it was the Hardy family who played a significant role in the introduction and development of this groundbreaking braking system. John Hardy, the father, began his journey in the railway industry by working for Robert Stephenson Hawkes and Co., establishing a direct connection to the earliest passenger-carrying railways. Building upon their father's experience, the sons, John George and William Edward Hardy, continued to advance the vacuum brake's development in Europe. They even manufactured components for vacuum braking systems in their own iron works, contributing to its widespread implementation. Despite the undeniable advantages of fail-safe vacuum brakes, their adoption faced resistance from major railway companies. The primary concern was the additional cost associated with implementing these safety measures. However, tragic avoidable accidents in the railway industry served as a wake-up call, leading to a progressive shift in perspective. The Armagh Rail Disaster: One particular incident stands out as a turning point in the mass adoption of fail-safe vacuum brakes—the Armagh rail disaster. On June 12, 1889, tragedy struck when a crowded Sunday school excursion train collided with a stationary locomotive at Armagh station. The devastating accident resulted in a high number of casualties, including many children. The aftermath of the Armagh rail disaster prompted a thorough investigation into the causes and subsequent safety reforms. The incident underscored the urgent need for fail-safe braking systems and led to significant improvements safety protocols. The vacuum brake system quickly became popular and was adopted by railways around the world. Although vacuum brakes have largely been replaced by more modern braking systems, their development marked a significant step forward in the history of rail transport, making trains safer, more reliable, and easier to operate.


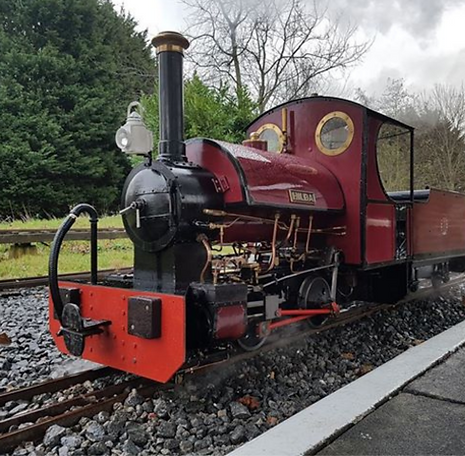
The guidance for passenger-carrying miniature railways is: Trains should have a braking system which is adequate for:
-
Loaded train weight
-
The normal speed of running
-
Gradients
-
Operating methods
The system is to be capable of bringing the train to a stop in a safe distance in normal and emergency conditions.
Based on these guidelines it is a must to fit an automatic (fail-safe) braking system on all your trains. Running without adequate braking could have serious consequences.



"Braking with Precison: What you need to consider"
As on full-size steam railways the two main types of braking systems for miniature railway locomotives and trains: are vacuum and compressed air. Although both systems have advantages and disadvantages, the vacuum is the most popular choice among miniature railway enthusiasts and model engineers.
Compressed air brakes, commonly used on full-size railways, work by using compressed air to apply force to the brake shoes or brake blocks on the wheels. It is a highly efficient and reliable system.
Advantages: High air pressure means only small brake cylinders are required which can easily be fitted into small spaces on vehicles. Air leaks are usually easy to trace.
Disadvantages: An air pump (compressor) is always required. Pressure vessels are required for reservoirs. Pressure connections are required on all pipe work.
In contrast, vacuum brakes, which were also widely used on full-size railways in the past, work by using atmospheric pressure to apply the brakes.
Advantages: On steam engines vacuum can be created by a very small ‘ejector’. No pressure vessels are required for reservoirs. Pipework and connections can be simple plastic push-on fittings.
Disadvantages: On none ejector-fitted locos a vacuum pump is required. Low air pressure means relatively large brake cylinders (actuators) are required which may be awkward to site. Leaks can be difficult to find.
Because of its inherent simplicity and since most miniature railways and model engineering societies have steam engines, the popular choice is the vacuum braking system.

"Unlocking the Mechanics of Vacuum Brakes"
-
The ejector or vacuum pump draws the air from the train pipe, the brake cylinder, and the reservoir (via the non-return valve). The brakes will then be off and the system will be in equilibrium.
-
The brakes will be kept off by being weight biased or lightly sprung. Please refer to the diagram.
-
Letting air back into the train pipe via the driver's brake valve or a pipe disconnection the air pressure acting on the underside of the piston or, in this case, the diaphragm, will push the piston up and pull on the brakes.
-
Since the vacuum on the upper side of the piston is trapped by the none return valve the vacuum must be recreated in the train pipe to release the brakes.
-
Similarly when the loco is removed and the brakes need to be released to shunt the train this trapped vacuum can be destroyed by opening the release valve.
How do Vacuum Brakes Work?
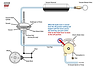


Click images to enlarge

"Vacuum Brakes: The Essential Components You Need!"
To fit vacuum brakes you will need several ancillary pieces of equipment. Some of this equipment includes:
Vacuum Brake Actuator - This is the main component of a vacuum brake system. It converts the vacuum pressure in the train pipe into a mechanical force that is used to apply the brakes on the train.
Vacuum Reservoir -The reservoir is a necessary component when fitting vacuum brakes. The reserve of vacuum (if there is such a thing) makes it possible to create the differential between it and atmospheric pressure to apply a force on the diaphragm, thus applying the brakes.
Vacuum Ejector - Is designed to create the most vacuum using the least amount of steam. Both provide a reliable and effective means of creating a vacuum on steam locomotives for powering the brake systems fitted to rolling stock.
Vacuum Pump - For electric or internal combustion locomotives, you will require a 12v Vacuum Pump.
Vacuum Limit Valve - For use on steam locomotives fitted with an ejector. It is used to set the highest limit of vacuum used in the system. Limiting the amount of vacuum is important because if the reservoir vacuum is ever higher than the vacuum achievable by the pump or ejector, the brakes will stay on and not come off.
Vacuum Gauges - While two gauges can be utilized, with one indicating the train pipe vacuum and the other displaying the vacuum in the locomotive reservoir, it's sufficient to have just one gauge for the train pipe.
Drivers Brake Valve: A suitable option for both electric and steam-powered vacuum systems is the progressive brake valve, which is particularly effective when used together with a vacuum pump. Alternatively, a combined vacuum and steam valve will for the operation of a locomotive steam brake and the application of the train vacuum brake with the same control handle.
Release Valve: The release value is employed to allow atmospheric pressure into the vacuum reservoir. To release a detached vehicle.
Brake Blocks: The brake blocks are the replaceable parts of the brake shoes that come in contact with the train wheels. They are made of friction material that helps to slow down or stop the train.
-
What do I use to create a vacuum?You will need either a vacuum pump or an ejector. For electric or internal combustion-powered locomotives, you will require a vacuum pump fitted to a train to evacuate the atmospheric pressure from the train pipe, reservoirs, and brake cylinders to keep the brakes off. It is usually controlled by the driver's brake valve. For creating a vacuum on steam locomotives, you will need an ejector. The ejector consists of a series of cones inside a tube. Steam can pass through the cones so that a vacuum is created in the main body and thus in the brake pipe to which it is connected. A vacuum pump can also be used instead of the ejector.
-
Why is it important to limit the vacuum in the system?If the reservoir vacuum is ever higher than the vacuum achievable by the pump or ejector, the brakes will stay on and not come off.
-
What do I use for the brakepipe?The vacuum brake system is controlled through a brake pipe (The train pipe) connected to a brake valve in the driver's cab. Each vehicle in the train should have at least one brake cylinder and vacuum reservoir. The train pipe can be a flexible PVC hose that runs the length of the train. It is connected between vehicles, which can be uncoupled when the locomotive and rolling stock separate. When separated the loss of vacuum will allow air at atmospheric pressure to apply the brakes, making the vehicles fail-safe. Releasing the vacuum in the reservoir side of the actuator with the release valve allows atmospheric pressure on both sides of the diaphragm, thus releasing the brakes.
-
How do I limit the amount of vacuum in the system?If your steam locomotive has been fitted with an ejector, fitting a vacuum limiting valve will allow you to set the highest limit of vacuum used in the system. This is usually 12" -15” of mercury, shown as Hg units on the vacuum gauge. An electric pump has a vacuum switch that can be set to the required vacuum level.
-
What is the difference between the standard brake kit and kit with trunnion mounting?The only difference between the kits is the way that the actuators can be mounted. The standard kit has a stud extending from the rear cover and the other with two bearings mounted at its mid-point. If space is at a premium, then the trunnion version is the better option. The kits are very easy to assemble, and no machining is required.
-
What are the brake blocks made from?All brake blocks are plastic injection moulded in a grade of nylon which is filled with glass beads to a level of 40%. The beads are very small and provide the braking medium with the plastic acting as the carrier. The plastic brake blocks bed into the wheels and remove traces of dirt and aluminum. They will also not attach to the wheels with rust.
-
What components do I need to fit vacuum brakes?There are of course many different types of locomotives and rolling stock so there is no generic answer. The solution shown below is based on a narrow-gauge Romulus hauling two eight-wheeled wagons. On the loco, all wheels are braked whilst on the wagons just the rear four-wheel bogie is braked.

-
What do I use to create a vacuum?You will need either a vacuum pump or an ejector. For electric or internal combustion-powered locomotives, you will require a vacuum pump fitted to a train to evacuate the atmospheric pressure from the train pipe, reservoirs, and brake cylinders to keep the brakes off. It is usually controlled by the driver's brake valve. For creating a vacuum on steam locomotives, you will need an ejector. The ejector consists of a series of cones inside a tube. Steam can pass through the cones so that a vacuum is created in the main body and thus in the brake pipe to which it is connected. A vacuum pump can also be used instead of the ejector.
-
Why is it important to limit the vacuum in the system?If the reservoir vacuum is ever higher than the vacuum achievable by the pump or ejector, the brakes will stay on and not come off.
-
What do I use for the brakepipe?The vacuum brake system is controlled through a brake pipe (The train pipe) connected to a brake valve in the driver's cab. Each vehicle in the train should have at least one brake cylinder and vacuum reservoir. The train pipe can be a flexible PVC hose that runs the length of the train. It is connected between vehicles, which can be uncoupled when the locomotive and rolling stock separate. When separated the loss of vacuum will allow air at atmospheric pressure to apply the brakes, making the vehicles fail-safe. Releasing the vacuum in the reservoir side of the actuator with the release valve allows atmospheric pressure on both sides of the diaphragm, thus releasing the brakes.
-
How do I limit the amount of vacuum in the system?If your steam locomotive has been fitted with an ejector, fitting a vacuum limiting valve will allow you to set the highest limit of vacuum used in the system. This is usually 12" -15” of mercury, shown as Hg units on the vacuum gauge. An electric pump has a vacuum switch that can be set to the required vacuum level.
-
What is the difference between the standard brake kit and kit with trunnion mounting?The only difference between the kits is the way that the actuators can be mounted. The standard kit has a stud extending from the rear cover and the other with two bearings mounted at its mid-point. If space is at a premium, then the trunnion version is the better option. The kits are very easy to assemble, and no machining is required.
-
What are the brake blocks made from?All brake blocks are plastic injection moulded in a grade of nylon which is filled with glass beads to a level of 40%. The beads are very small and provide the braking medium with the plastic acting as the carrier. The plastic brake blocks bed into the wheels and remove traces of dirt and aluminum. They will also not attach to the wheels with rust.
-
What components do I need to fit vacuum brakes?There are of course many different types of locomotives and rolling stock so there is no generic answer. The solution shown below is based on a narrow-gauge Romulus hauling two eight-wheeled wagons. On the loco, all wheels are braked whilst on the wagons just the rear four-wheel bogie is braked.

Join the PNP Railways Club
For the Lastest Product News & Special Offers